Preventive maintenance is an essential aspect of any company’s operations. Unfortunately, it often gets overlooked in favor of reactive maintenance or repairs. This approach can be costly in the long run, not only in terms of finances but also in terms of lost productivity and downtime. Here we’ll discuss what preventive maintenance is and why it’s crucial for a company’s bottom line. We’ll also explain how facility managers play a crucial role in keeping equipment well maintained, and how Data Fleet’s Facility AI software can help them do that.
The Importance of Routine Checkups
Regular equipment inspections reduce the probability of unexpected failures and associated costs and improve your asset information management (AIM) platform experience. When a company’s facility manager knows precisely when a piece of equipment is in need of maintenance, they can schedule preventive maintenance before the equipment fails. By scheduling maintenance, a company can maximize its equipment’s lifespan while minimizing downtime. This is good news for both facility managers and the organization as a whole.
Routine checkups or preventive maintenance of equipment are crucial for several reasons:
- Prevents Unexpected Equipment Failures:
Regular inspections allow for identification and correction of minor issues before they escalate into major problems. This can significantly reduce the likelihood of unexpected equipment failures, which often lead to costly repairs and extended downtime. - Extends Equipment Lifespan:
By addressing potential problems early, routine checkups can help extend the lifespan of equipment, thereby maximizing the return on investment. - Enhances Safety:
Regular maintenance ensures that all safety mechanisms are functioning properly, reducing the risk of accidents and injuries. - Improves Efficiency:
Well-maintained equipment tends to operate more efficiently, leading to improved productivity and cost savings. - Complies with Regulations:
In many industries, regular equipment inspections are a regulatory requirement. Routine checkups help ensure compliance, avoiding potential fines or other penalties.
In short, routine checkups for preventive maintenance are an essential part of managing equipment and enhancing your AIM platform experience. By reducing the probability of unexpected failures and associated costs, they can help improve efficiency, safety, and regulatory compliance, while extending the lifespan of your equipment.
Predictive Maintenance Analytics Is Your New Best Friend
One of the most powerful features of Data Fleet’s Facility AI software is its predictive maintenance analytics that can provide insight into an asset’s current state of degradation based on its remaining useful life and when correlated to historical data for like assets. This insight helps facility managers schedule maintenance tasks before the equipment breaks down by alerting operators when it may need to be replaced.
Predictive analytics uses machine learning tech (better known as A.I.) and other related external data sources such as manufacture date, last maintenance date, etc. to predict when equipment is at risk of failure, which decreases the chance of a catastrophic unscheduled failure. The software will recommend preventive maintenance intervals for equipment, allowing facility managers to anticipate equipment problems and fix or replace them before they escalate into expensive repairs. This prevents disruptions in production, saves on repair costs, and provides useful information for capital planning.
In addition, Facility AI predictive maintenance analytics can greatly enhance the functionality of your AIM (asset information management) and CMMS platforms:
- Improved Data Accuracy:
Regularly updating equipment status and condition in your AIM platform ensures that you have accurate, up-to-date information at your fingertips. This can support better decision-making and capital planning. - Predictive Maintenance:
With consistent data from routine inspections, your AIM platform can help predict when equipment might fail and schedule maintenance accordingly. This predictive maintenance approach can further reduce the likelihood of unexpected equipment failures and associated costs. - Enhanced Asset Tracking:
When integrated with a CMMS, an AIM platform can track the history of each asset, including all inspections and maintenance activities. This can help identify trends, such as recurring problems, and facilitate strategic planning for equipment replacement or upgrades. - Cost Control:
Accurate tracking of maintenance activities and costs in your AIM platform can help identify opportunities for cost savings, such as unnecessary maintenance or inefficient equipment.
Staff Training Is Key
Finally, it is also essential to train staff in preventive maintenance. A properly trained team can spot potential issues early, preventing major repairs. With Facility AI, the system will help provide your team with recommended preventive maintenance schedules.
Staff members should know what kind of maintenance action to take and when to take it. They should be aware of the importance of preventive maintenance and the consequences of ignoring it. By training your staff in preventive maintenance, complimented with Predictive Maintenance capabilities, you’ll improve your equipment’s performance, reduce your maintenance expenses, and ensure that your facility is operating at maximum efficiency.
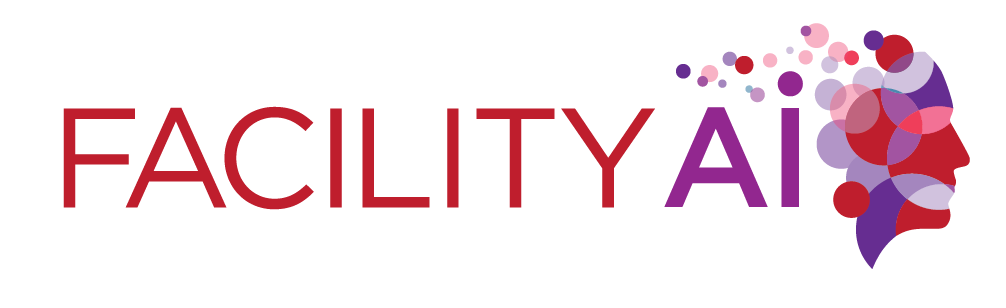